Production-Scale Metal AM on the Move
New survey from Additive Manufacturing Research digs into adoption progress for metal AM for full-scale production.
Latest News
January 12, 2024
Metal AM continues to gain mainstream momentum for production applications, according to a new global survey by Additive Manufacturing Research.
The benefits of metal AM are widely recognized across industries with nearly 80% confirming they are utilizing the technology with an array of materials, including titanium, steel, aluminum, and nickel alloy. The number of parts produced is still on the lower end—41% are outputting less than 50 parts annually while 9% are building between 500 and 1,000 AM parts per year and 11% currently executing between 1,000 and 10,000 AM-enabled parts each year.
While metal material choices have grown over substantially, users are still seeking a broader selection to enhance performance beyond their current needs. There is more emphasis put on sustainability with organizations expressing a desire for better solutions that enhance materials handling and minimize scrap. While 85% of respondents to the AMR survey said currently available metal materials met their requirements, nearly a third were still in search of additional unique alloys. Moreover, 27% of respondents were seeking materials with increased strength with 21% on the lookout for metal AM materials options with reduced weight properties.
Fifty-eight percent of those responding to the AMR survey said they handle scrap differently with AM than conventional production methods, with 39% confirming they are looking for alternative ways to handle failed prints, scrap, and unused powder in pursuit of greater sustainability.
When evaluating metal AM materials for purchase, survey respondents said they prioritize consistency and quality, both for the material itself as well as batch-to-batch consistency. The price of materials isn’t as much of a barrier for respondents—less than a third (29%) called out cost as a major factor when making materials purchasing decisions. Other important considerations: Rapid availability and lead time of materials, supplier reputation and customer service, and quality and consistency of metal powder.
Go to this link to download the full survey.
Subscribe to our FREE magazine,
FREE email newsletters or both!Latest News
About the Author

Beth Stackpole is a contributing editor to Digital Engineering. Send e-mail about this article to [email protected].
Follow DE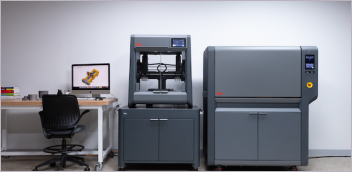
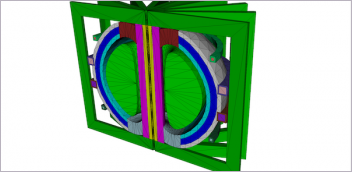
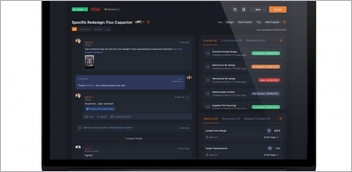
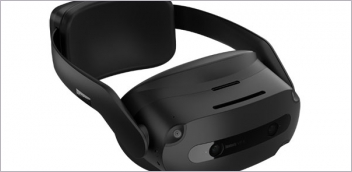